Introduction
In today's modern world, electricity plays a crucial role in powering various industries, businesses, and households. However, power outages and blackouts are common occurrences that can disrupt daily operations and cause significant financial losses. To combat these issues, many businesses and organizations rely on diesel generators as a reliable backup power source. Diesel generators are known for their durability, efficiency, and reliability, making them a popular choice for ensuring uninterrupted power supply. In this article, we will explore the importance of quality assurance in diesel generators and how it contributes to their overall performance and reliability.
Overview of Diesel Generators
Diesel generators are power generation systems that use diesel fuel to produce electricity. They consist of an engine, alternator, fuel system, cooling system, and control panel. The diesel engine drives the alternator, which generates electrical power. Diesel generators are available in various sizes and configurations to meet different power requirements, from small portable units for residential use to large industrial generators for commercial and industrial applications.
One of the key advantages of diesel generators is their fuel efficiency and cost-effectiveness. Diesel fuel is less expensive than gasoline and other fuels, making diesel generators a cost-effective choice for long-term use. Additionally, diesel engines are known for their durability and longevity, requiring less maintenance compared to other types of generators. This makes diesel generators a reliable and practical choice for backup power generation.
Importance of Quality Assurance in Diesel Generators
Quality assurance is a critical aspect of ensuring the performance, reliability, and safety of diesel generators. Quality assurance encompasses a set of processes and procedures that are implemented to maintain the quality and consistency of products or services. In the case of diesel generators, quality assurance involves rigorous testing, inspection, and monitoring to ensure that the generator meets industry standards and specifications.
There are several reasons why quality assurance is essential for diesel generators:
1. Reliability: Diesel generators are often used as backup power sources in critical applications where power outages can have severe consequences. Ensuring the reliability of diesel generators through quality assurance processes helps minimize the risk of generator failure and ensures continuous power supply when needed.
2. Performance: Quality assurance measures such as testing and inspection help identify any performance issues or defects in diesel generators. By addressing these issues early on, manufacturers can improve the overall performance of the generator and optimize its efficiency.
3. Safety: Diesel generators operate using flammable fuel and generate high voltages, making safety a top priority. Quality assurance processes help identify potential safety hazards and ensure that the generator meets safety standards to protect users and equipment from harm.
4. Compliance: Diesel generators are subject to various regulations and standards set by industry bodies and government authorities. Quality assurance ensures that the generator complies with these regulations, avoiding potential legal issues and penalties.
Quality Assurance Processes for Diesel Generators
Quality assurance for diesel generators involves a series of processes and procedures that are implemented throughout the design, manufacturing, testing, and maintenance phases. The following are some key quality assurance processes for diesel generators:
1. Design Review: The design of a diesel generator is a critical factor that determines its performance, efficiency, and reliability. Design reviews involve a thorough evaluation of the generator's components, specifications, and layout to identify any potential design flaws or weaknesses. By conducting design reviews, manufacturers can optimize the design of the generator and ensure that it meets the required standards.
2. Material Inspection: Quality assurance begins with the inspection of raw materials and components used in the manufacturing of diesel generators. Manufacturers must ensure that all materials meet quality standards and specifications to prevent defects and malfunctions in the generator.
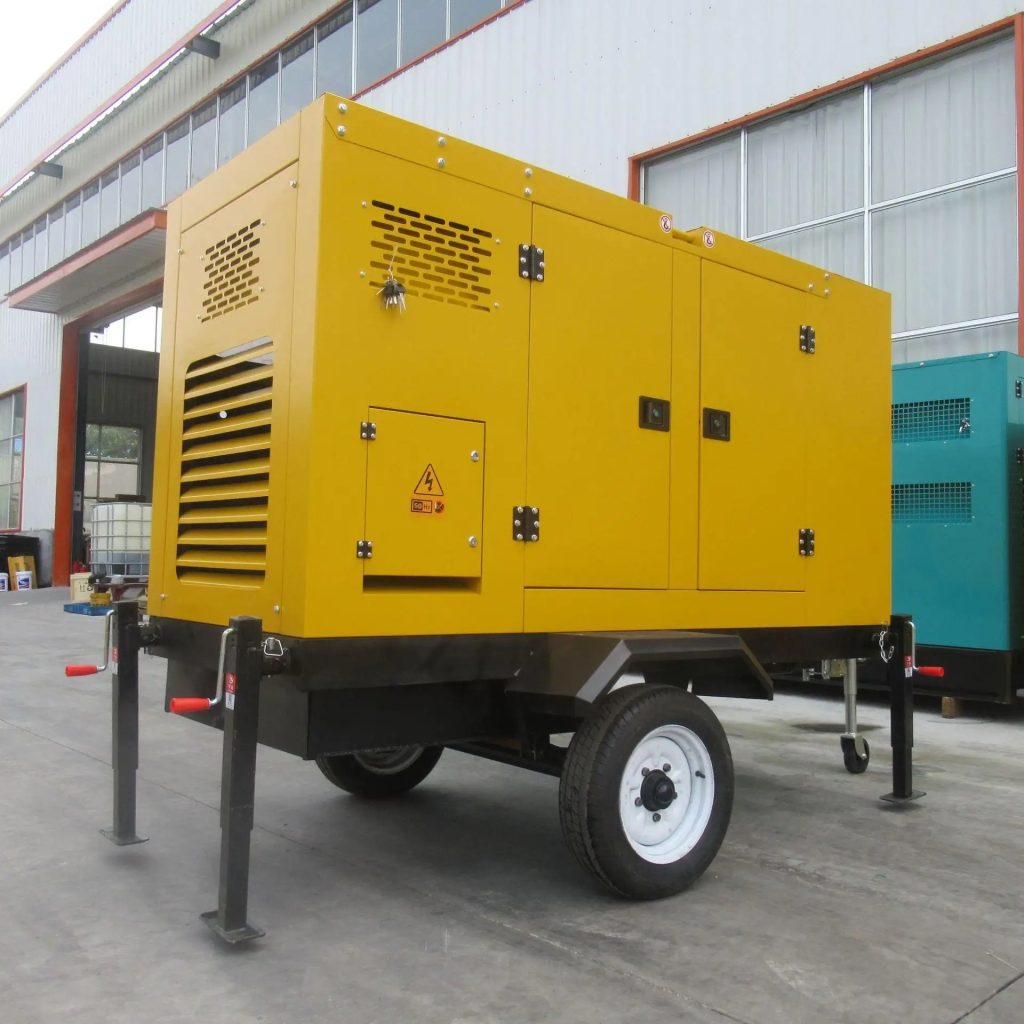
3. Manufacturing Process Control: During the manufacturing process, quality assurance measures such as process control and quality control are implemented to monitor and evaluate the production of diesel generators. Manufacturers must maintain strict control over manufacturing processes to ensure consistency and quality in the final product.
4. Testing and Validation: Testing and validation are essential steps in quality assurance for diesel generators. Various tests, such as performance testing, load testing, and safety testing, are conducted to verify the functionality and reliability of the generator. Testing helps identify any defects or issues that need to be addressed before the generator is deployed in the field.
5. Maintenance and Service: Quality assurance does not end with the manufacturing of the generator. Regular maintenance and service are crucial for ensuring the continued performance and reliability of diesel generators. Manufacturers provide maintenance guidelines and service schedules to help users maintain their generators in optimal condition.
Benefits of Quality Assurance in Diesel Generators
Implementing quality assurance processes in the design, manufacturing, and maintenance of diesel generators offers several benefits for manufacturers, users, and the environment. Some of the key benefits of quality assurance in diesel generators include:
1. Improved Energy-saving tips for using a 400kW generator : Quality assurance helps identify and address potential issues in diesel generators, improving their reliability and reducing the risk of unexpected failures. This ensures that the generator can provide continuous power supply when needed, especially in critical applications.
2. Enhanced Performance: By optimizing the design and manufacturing processes, quality assurance can improve the performance and efficiency of diesel generators. This results in better fuel efficiency, reduced emissions, and overall improved performance of the generator.
3. Increased Safety: Quality assurance processes help ensure that diesel generators meet safety standards and regulations, protecting users and equipment from potential hazards. This reduces the risk of accidents and injuries associated with generator operation.
4. Cost Savings: Quality assurance helps prevent defects and malfunctions in diesel generators, reducing the need for costly repairs and downtime. By investing in quality assurance, manufacturers and users can save money in the long run and avoid unnecessary expenses.
5. Compliance with Regulations: Diesel generators are subject to various regulations and standards that govern their design, manufacturing, and operation. Quality assurance processes ensure that the generator complies with these regulations, avoiding legal issues and penalties.
Conclusion
In conclusion, quality assurance is a vital aspect of ensuring the performance, reliability, and safety of diesel generators. By implementing quality assurance processes throughout the design, manufacturing, and maintenance phases, manufacturers can produce high-quality generators that meet industry standards and user requirements. Quality assurance helps improve the reliability, performance, and safety of diesel generators, making them a dependable backup power source for various applications. Investing in quality assurance not only benefits manufacturers by enhancing their products but also provides users with a reliable and efficient power generation solution. Diesel generators will continue to play a crucial role in ensuring uninterrupted power supply in a world where electricity is essential for daily operations.